Efficiency and performance are key factors in the success of any crushing and screening operation. By implementing best practices, businesses can optimize their processes, minimize downtime, and achieve superior results. In this blog post, we will explore essential best practices that can help you maximize efficiency and performance in your crushing and screening operations.
Proper Equipment Selection
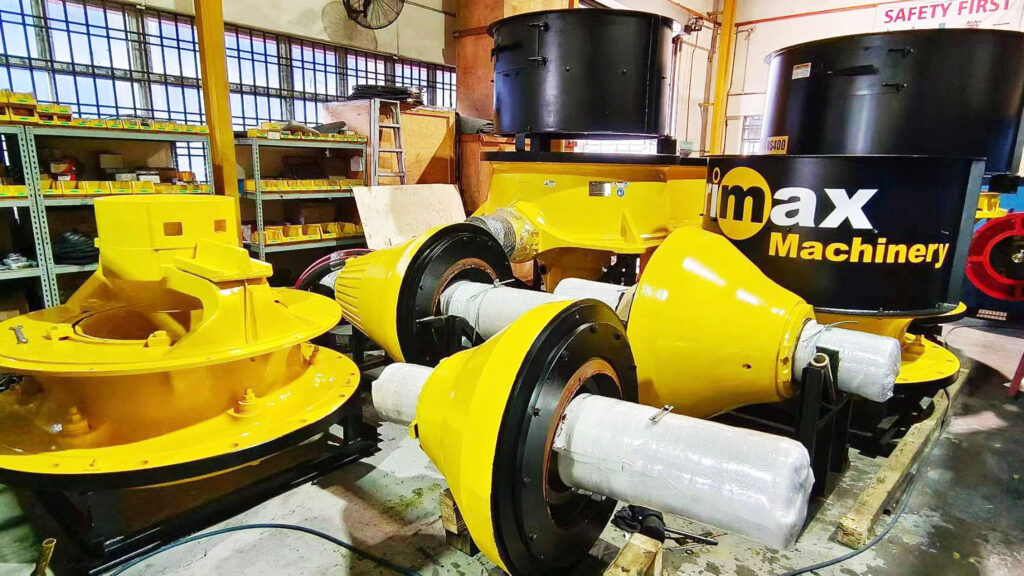
Choosing the right equipment is crucial for efficient crushing and screening. For example, if you’re dealing with abrasive materials like granite or quartzite, selecting a jaw crusher with robust construction and installed with liners with high wear resistance can prevent premature wear and reduce downtime. On the other hand, if you’re processing softer materials like limestone, a horizontal shaft impactor or HSI might be a more suitable option.
If product shape is a concern, then consider multiple stages of crushing with cone crushers and vertical shaft impactors (VSIs). Cone crushers and vertical shaft impactors (VSIs) excel in producing cubical and well-graded final products, making them ideal for applications where precise shaping and fine aggregates are required. On the other hand, crushing with only a single jaw crusher or with more than 1 stage of crushing with jaw crushers would not be able to achieve the desired result. In certain circumstances, up to 4 stages of crushing may be required if desired product shape is of utmost importance. If the aim is to obtain large quantities of fine minerals 3mm and below, then a ball mill or several ball mills may be required in order to achieve the required production capacity.
Additionally, consider the size and capacity of the equipment to match your production requirements. Oversized equipment can result in inefficient operation, while undersized equipment may struggle to meet the desired production targets.
In conclusion, proper equipment selection is critical for achieving efficient crushing and screening operations. By considering factors such as material characteristics, output requirements, and production capacity, you can ensure that the chosen equipment is optimized for performance, durability, and productivity, leading to better outcomes and improved profitability. Consulting with experts and relying on reputable manufacturers like Trimax Machinery can provide valuable guidance and help you make informed decisions for your specific application needs.
Regular Equipment Maintenance
Regular maintenance is vital to keep your equipment in peak condition and ensuring its longevity. Here are some key aspects to consider when implementing a regular equipment maintenance routine: –
- Create a maintenance schedule: Develop a comprehensive maintenance schedule that outlines the specific tasks and intervals for maintenance activities. This schedule should cover routine inspections, lubrication, cleaning, adjustments, and components or parts replacements.
- Conduct routine inspections: Regularly inspect your equipment to identify any signs of wear, damage, or potential issues. Look for loose or damaged parts, leaks, unusual noises, or abnormal vibrations. Promptly address any problems discovered during inspections to prevent further damage and minimize downtime.
- Lubrication: Proper lubrication is vital for smooth operation of mechanical components. Follow the manufacturer’s recommendations for lubrication intervals and use the recommended lubricants. Pay special attention to bearings, gears, and other moving parts that require lubrication to prevent excessive friction and wear.
- Clean equipment regularly: Dust, debris, and build-up can negatively impact equipment performance and lead to premature wear. Clean your equipment regularly, both externally and internally. Use appropriate cleaning techniques and tools to remove dirt, grime, and contaminants. Ensure that cleaning does not introduce moisture or damage sensitive components.
- Replace worn parts: Components subjected to high levels of wear, such as v-belts, filters, and screening media, should be regularly inspected and replaced as needed. Follow the manufacturer’s guidelines and consider keeping a stock of commonly required spare parts to minimize downtime.
- Document maintenance activities: Maintain a record of all maintenance activities, including dates, tasks performed, and any issues encountered. This documentation helps track the maintenance history, identify recurring problems, and schedule future maintenance tasks effectively.
- Train and empower maintenance personnel: Ensure that your maintenance personnel are properly trained on equipment maintenance. Provide them with the necessary tools, resources, and access to technical documentation. Encourage a proactive approach to maintenance by empowering them to report and address issues promptly.
- Collaborate with equipment manufacturers: Stay in touch with the equipment manufacturers or authorized service providers. They can provide guidance on maintenance best practices, offer technical support, and inform you of any updates, recalls , or recommended improvements related to your equipment.
Optimal Material Handling
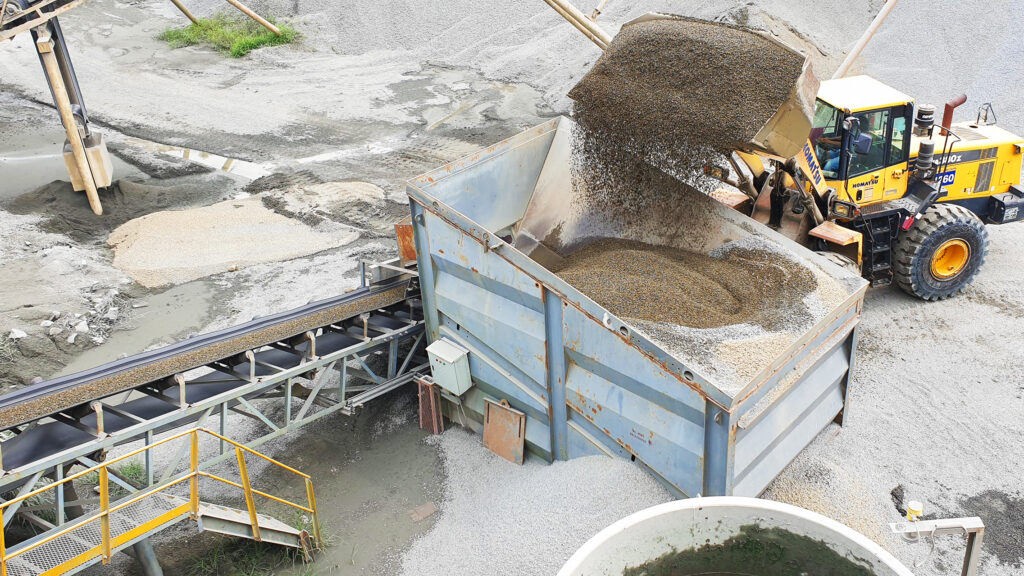
Efficient material handling is vital for smooth productive crushing and screening operations. Here are some key considerations for achieving optimal material handling: –
- Proper loading and feeding techniques: Implement proper loading and feeding techniques to ensure a continuous and consistent flow of material. Avoid overloading or underloading the equipment. Use equipment such as dump trucks, loaders or excavators with appropriate capacities or bucket sizes to match the production capacity of the crushing and screening plant.
- Grizzly feeders and scalping screens: Consider utilizing grizzly feeders or scalping screens whenever necessary, to remove fines, undersized material, and contaminants. These equipment help to ensure that only the desired material enters the crushing process, preventing unnecessary wear on the equipment downstream and improving overall efficiency.
- Conveyor systems: Utilize efficient conveyor systems to transport material between various stages of the crushing and screening process. Conveyor belts should be appropriately sized and designed for the specific application, considering factors such as material weight, lump size, and throughput requirements. Ensure proper belt tension, alignment, and regular maintenance to prevent spillage, mis-tracking, and unplanned downtime.
- Minimize re-handling: Minimizing re-handling of material reduces labor requirements and improves operational efficiency. Design the layout of your crushing and screening plant to minimize the need for excessive material movement. Consider the strategic positioning of equipment, conveyors, and stockpiles to optimize the flow of material and minimize unnecessary handling.
- Stockpile management: Effective stockpile management is crucial for maintaining material quality and ensuring a consistent feed to the crushing and screening equipment. Proper stockpile construction, such as layering and compacting material, prevents segregation and maintains material homogeneity. Implement a systematic approach to material rotation to prevent stockpile degradation and ensure the use of the oldest material first.
- Dust suppression: Dust generation is a common issue in material handling operations. Implement appropriate dust suppression measures, such as water sprays or dust collection systems, to minimize airborne dust. Controlling dust not only creates a safer working environment but also improves equipment performance by reducing the risk of equipment clogging and minimizing wear.
Effective Screening Practices
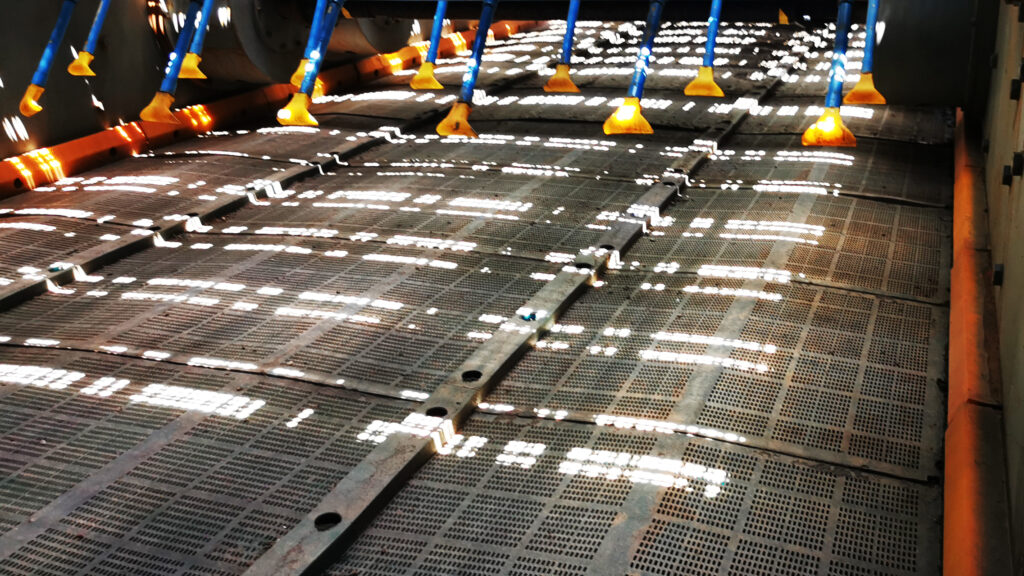
Screening is a critical step in the crushing and screening process as it separates the desired product from undersized or oversized material. Implementing effective screening practices can significantly enhance the efficiency and quality of your operations. Here are some key considerations for achieving effective screening: –
- Select the right screen media: Choose the appropriate screen media for your specific application. Different materials have varying characteristics, such as abrasiveness, moisture content, and particle size distribution. Consider factors like screen opening size, wire diameter, and wire diameter, and material type (such as woven wire cloth, polyurethane, rubber, or perforated plate) to optimize screening efficiency and ensure accurate separation of materials.
- Optimize screen vibration: The vibration of the screen affects material flow and screening efficiency. Experiment by adjusting vibration parameters such as amplitude and frequency, to optimize the movement and stratification of material on the screen deck, ensuring effective screening and maximum throughput.
- Regularly inspect and clean screens: Regularly inspect the screens for wear, tears, or blockages. Clean the screens to remove any build-up, blinding, or clogging that can hinder the screening process.
- Consider multiple deck configurations or multiple vibrating screens: Multi-deck screens or multiple vibrating screens can provide additional screening stages and enhance the efficiency of the process. By using multiple decks with different screen media or opening sizes, you can achieve more precise classification and separation of materials, resulting in improved product quality.
- Optimize screen throughput: Adjust the feed rate to the screen to optimize throughput while avoiding overloading or underloading. Maintaining the ideal balance between the feed rate and screen capacity ensures efficient screening and prevents excessive wear or inefficiencies.
Utilization of Automation and Technology
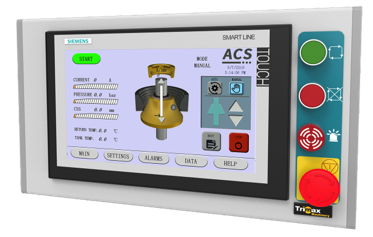
Leverage automation and technology to enhance efficiency and performance. Advanced control systems such as PLC, real-time monitoring such as belt scales, and performance optimization such as crusher automation control systems. Embrace technologies like remote monitoring with closed circuit cameras, condition monitoring sensors, and machine learning algorithms to identify potential issues and optimize equipment performance.
Employee Training and Safety
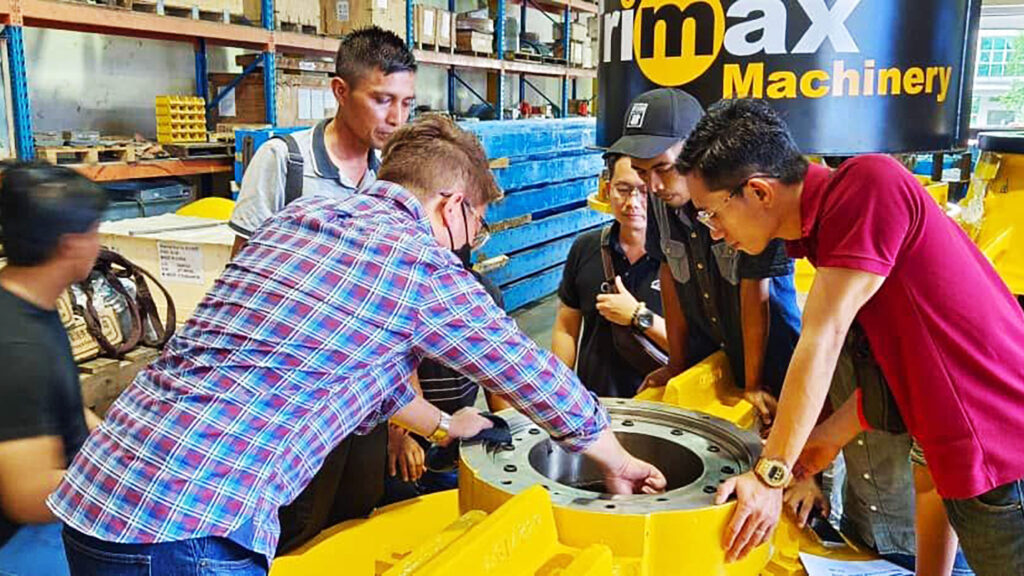
Employee training and safety are paramount in any crushing and screening operation. Prioritizing comprehensive training programs and robust safety measures can contribute to a safe and productive work environment. Here are key aspects to consider when focusing on employee training and safety: –
- Safety training programs: Develop and implement safety training programs that covers al aspects of the job, including equipment operation, hazard identification, emergency procedures, and proper use of personal protective equipment (PPE). Conduct regular safety meetings and refresher training sessions to reinforce safe work practices and ensure compliance with safety regulations.
- Equipment-specific training: Provide thorough training on the safe and proper operation of all equipment used in the crushing and screening process. This includes training on start-up and shutdown procedures, equipment adjustments, maintenance protocols, and troubleshooting techniques. Ensure that operators are well-versed in equipment limitations and safety features.
- Hazard identification and risk assessment: Training employees to identify potential hazards and assess risks associated with specific tasks or work areas. Encourage them to report any safety concerns promptly. Conduct regular risk assessments to identify areas for improvements and implement necessary control measures to mitigate risks.
- Safe work procedures: Establish clear and standardized safe work procedures for all tasks performed in the crushing and screening operation. This includes guidelines for equipment operation, maintenance activities, material handling, and working at heights. Ensure that employees understand and follow these procedures to minimize the risk of accidents and injuries.
- Personal protective equipment (PPE): Provide appropriate PPE, such as hard hats, safety goggles, ear protection, gloves, and safety vests, to employees based on the job roles and the identified hazards. Train employees on the correct use, maintenance, and storage of PPE, and enforce its consistent use in the workplace.
- Emergency response and evacuation plans: Develop comprehensive emergency response and evacuation plans that cover various scenarios, including equipment malfunctions, fires, or medical emergencies. Conduct drills and training exercises regularly to ensure that employees are familiar with the procedures and can respond effectively in emergency situations.
- Ongoing safety culture: Foster a safety culture within the organization by encouraging open communication, active participation, and continuous improvement. Involve employees in safety committees or safety improvement initiatives, and recognize and reward safe work practices. Regularly assess the effectiveness of safety measures and seek feedback from employees to identify areas for improvement.
By proritizing employee training and safety, you create a work environment that promotes the well-being of your employees and reduces the risk of accidents and injuries. Thorough safety training programs, hazard identification, risk assessments, safe work procedures, proper use of PPE, emergency response plans, and fostering a strong safety culture all contribute to a safe and productive workplace in your crushing and screening operations.
Conclusion
In conclusion, optimizing your crushing and screening operations requires a holistic approach that encompasses various key factors. Proper equipment selection, regular equipment maintenance, optimal material handling, effective screening practices, utilization of automation and technology, and employee training and safety, all play crucial roles in achieving efficiency, productivity, and high-quality outcomes.
Incorporating these key considerations into your crushing and screening operations will not only enhance and productivity but also lead to better quality end products, cost savings, and a safer work environment.
As you strive for excellence in your crushing and screening operations, remember to regularly assess and optimize each aspect, stay updated on technological advancements, and embrace a continuous improvement mindset. By doing so, you can stay ahead in the industry and achieve long-term success.